Na pokazach, targach i konferencjach przy ich stanowisku zawsze jest tłumnie. Każdy chce zobaczyć, jak niewielkie urządzenie drukuje zakładkę do książki, Yodę z Gwiezdnych Wojen albo czyjąś twarz. Ale pokazy drukarek 3D to tylko niewielka część działalności studentów z koła naukowego Rapid Troopers
Cały świat oszalał na punkcie drukarek 3D. Media prześcigają się w testowaniu tych urządzeń i pokazywaniu kolejnych przedmiotów, które spod nich wyszły. Z każdym tygodniem zwiększa się zastosowanie drukarek 3D. Pomagają już pacjentom, u których konieczny był przeszczep twarzy i osobom, które straciły rękę. Architektom dostarczają elementy do ich makiet, przemysłowcom prototypy nowych konstrukcji, a dla fascynatów tej technologii są niekończącym się źródłem prób, testów i doświadczeń. Przy ich użyciu drukują już m.in. sukienki, buty, a nawet ciastka (podobno bardzo smaczne). W zeszłym roku świat obiegła wiadomość o Japończyku skazanym za wyprodukowanie w swojej drukarce w pełni sprawnego pistoletu. Do sądu trafił więc za nielegalne posiadanie broni.

Tysiące ludzi na całym świecie zleca też wydrukowanie swoich podobizn, chcąc postawić je na biurku albo podarować bliskiej osobie. Podobno to lepszy prezent niż wychodzące już z mody zdjęcie oprawiane w ramkę czy wkładane do portfela.
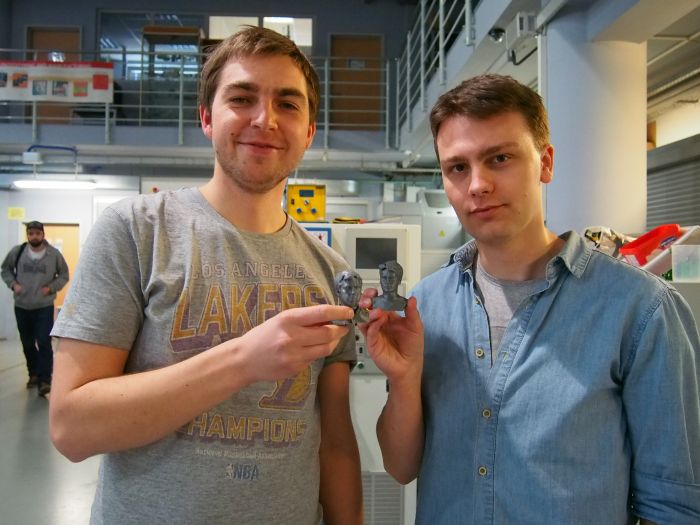
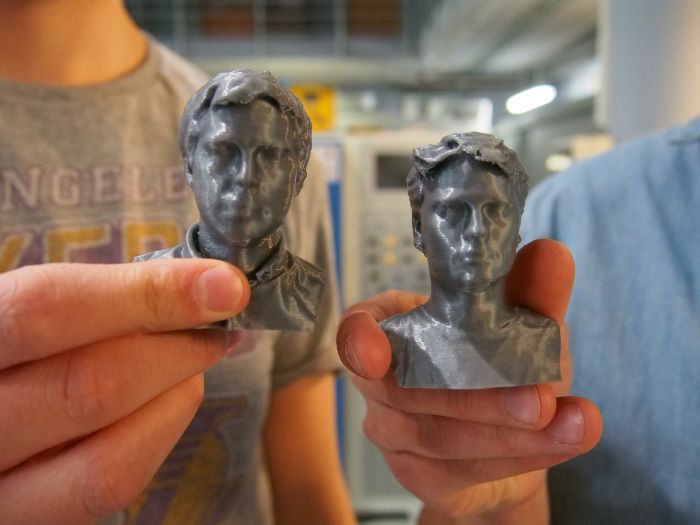
17 gramów w ponad godzinę
Ja także miałam okazję wyprodukować swoją twarz w drukarce 3D. Najpierw specjalny skaner zeskanował moją sylwetkę, by po chwili pokazać jej obraz 3D na komputerowym monitorze. Wydruk mojej podobizny na drukarce należącej do koła naukowego Rapid Troopers zająłby godzinę i 17 minut. Miałaby trochę ponad 5,5 cm wysokości i ważyłaby 17 gramów.
- Większe przedmioty wymagają czasu, ale wydrukowanie zakładki do książki to kwestia zaledwie kilkudziesięciu sekund – opowiada Jakub Karkocha z Rapid Troopers, który zaprosił mnie do boksu studenckiego koła naukowego działającego w budynku B4 na Politechnice Wrocławskiej. W warsztacie jest już kilka drukarek 3D, a wkrótce pojawią się kolejne. Każda została od podstaw złożona przez członków Rapid Troopers. Bo choć koło powszechnie kojarzy się pokazami druku 3D, to są one tylko niewielkim elementem jego działalności. Studenci przede wszystkim budują te urządzenia i testują ich możliwości.
W tej chwili w kole powstaje m.in. niskobudżetowa drukarka wykorzystująca technologię stereolitografii, drukująca przedmioty z warstw światłoczułej żywicy poliestrowej. Takie urządzenia w komercyjnej sprzedaży kosztują ponad 100 tys. zł. – My zamierzamy stworzyć je za około siedem tysięcy złotych – opowiada Daniel Marynowski. – Początkowo planowaliśmy, że wykorzystamy w niej diody z Xboxa, ostatecznie zdecydowaliśmy się na kupienie lasera o długości fali 405 nanometrów i mocy 100 mW.
Drukarka RepRap SLA w swojej górnej części będzie miała pojemnik z materiałem, a przedmioty drukowane w niej będą powstawały na platformie, która w miarę tworzenia wydruku będzie się podnosiła (model będzie tam budowany do góry nogami). Od dołu warstwy żywicy będą utwardzane wiązką lasera. Drukarka nie będzie najszybsza, ale za to bardzo dokładna. Będzie więc pozwalała na przygotowanie dość skomplikowanych wydruków.
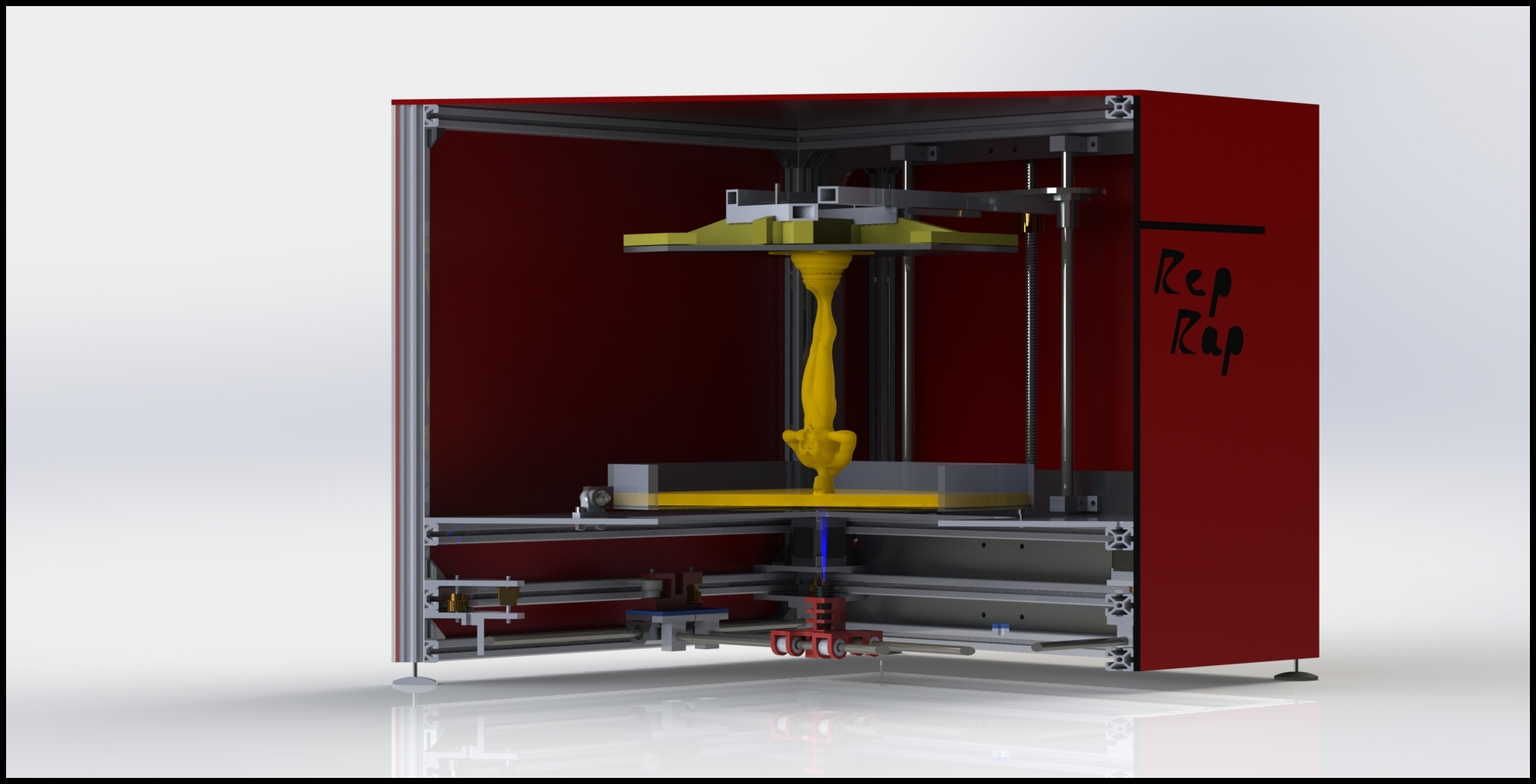
- Inspiracją dla RepRap SLA było skonstruowanie przez rosyjskiego inżyniera Mikhaila Shevchenko kompaktowego urządzenia, w którym wykorzystał m.in. części ze starego komputera – dodaje Daniel. - Jakość wydruków tej drukarki była jednak kiepska. Postanowiliśmy, że zrobimy to lepiej.
Kolejne drukarki już się tworzą
Członkowie Rapid Troopers pracują także nad przebudowaniem swojej pierwszej drukarki – RepRap 1. Powstała pięć lat temu i była wówczas pierwszym reprapem w Polsce, czyli urządzeniem samoreplikującym. Oznacza to, że jej poszczególne elementy zostały wydrukowane przez inną drukarkę. Po przebudowie ma służyć nowym członkom koła naukowego, którzy będą się na niej uczyć. – Jest prosta konstrukcyjnie, więc jeśli coś się w niej zepsuje, łatwo będzie to naprawić – tłumaczy Jakub Karkocha. – Bardziej zawansowane są w niej jedynie silniki, poza tym ma uniwersalną płytkę elektroniczną i elementy, które można kupić w markecie budowlanym. Jest więc naprawdę prosta do skonstruowania i naprawiania.
Jakub pokazuje także RepRapa 2.0. To drukarka, która ma dwie dysze, jedna drukuje z materiału modelowego, druga z podporowego. Z pierwszego powstaje właściwy przedmiot, drugi podtrzymuje wystające fragmenty, a po stwardnieniu materiału modelowego jest usuwany.
Ta drukarka będzie też większa od dotychczasowych urządzeń Rapid Troopers i będzie miała podgrzewaną komorę o wymiarach 300 x 300 x 500 mm. – Komora jest bardzo ważna dla jakości wydruków – tłumaczy Jakub. – Drukarka tworzy przedmiot, topiąc materiał w temperaturze około 210 stopni C. Tymczasem w otoczeniu jest około 20 stopni. Materiał doznaje więc szoku termicznego, zaczyna się kurczyć, zwija rogi, odkleja od platformy. Żeby to zminimalizować, podgrzewamy platformę i dopiero z czasem stopniowo ją schładzamy. Nie jest to jednak rozwiązanie idealne. Jeden z podstawowych materiałów do druku 3D – ABS jest dość wrażliwy na zmiany temperatury. Nie sposób wydrukować z niego przedmiotu o większej powierzchni, bo warstwy materiału odklejają się albo pękają. Podgrzewana komora zapobiegnie temu problemowi.
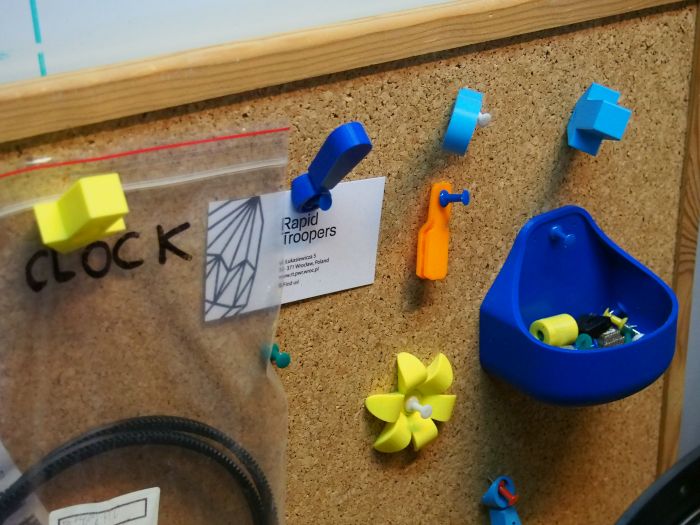
Jednym z projektów powstających w Rapid Troopers jest też głowica do drukowania z czekolady. W założeniu ma być wymienna, a to znaczy, że będzie ją można zamontować w drukarce, która na co dzień drukuje z tworzyw sztucznych.
Mosiądz z 80 proc. mosiądzu
Poza budowaniem nowych drukarek członkowie koła wykonują też zlecenia dla innych kół naukowych (np. drukowali elementy potrzebne do najnowszego łazika marsjańskiego ScorpioN) oraz testują materiały używane do wydruków. Standardowo stosuje się PLA i ABS. PLA to kwas polimlekowy, ABS jest natomiast kopolimerem akrylonitrylo-butadieno-styrenowym. Oba są zatem tworzywami sztucznymi, a dla przeciętnego człowieka po prostu plastikiem.
Coraz częściej jednak do wydruków 3D używa się także mieszanek różnych materiałów, dzięki czemu powstające z nich produkty wyglądają jak np. z drewna albo metalu. Dzieje się tak dzięki temu, że producenci oferują już materiały składające się przykładowo z 80 proc. brązu i 20 proc. PLA. Na rynku można już kupić m.in. materiały imitujące drewno, gumę, mosiądz, miedź czy gips. Są także takie z dodatkiem nylonu, które można później barwić typowymi barwnikami.
- Jako koło proponujemy badania właściwości termicznych i mechanicznych takich materiałów – opowiada Michał Olejarczyk, prezes koła. – Dzięki temu możliwe będzie tworzenie z nich nie tylko przedmiotów ozdobnych, ale i np. elementów inżynierskich. Wiadomo bowiem będzie, jaką mają np. wytrzymałość na ciężar.
Studenci badają wytrzymałość mechaniczną próbą rozciągania, czyli umieszczają próbki o jednakowej wielkości i wymiarach w maszynie wytrzymałościowej. Specjalne szczęki rozciągają je z odpowiednią prędkością aż pękną, a program komputerowy podaje wartości dla konkretnego nacisku na próbkę.
Dzięki badaniom studenci potwierdzili m.in., że wytrzymałość mechaniczna wydrukowanych elementów zależy od temperatury, w jakiej tłoczony był materiał. Dzięki pomiarowi tzw. wskaźnika płynięcia tworzywa są nawet w stanie wskazać optymalną temperaturę dla wytłaczania danego materiału, tak by przedmioty wydrukowane z niego były jak najwytrzymalsze.
- Oferujemy takie badania firmom produkującym materiały. Dzięki temu i my, i producenci możemy sporo dowiedzieć się i nauczyć o tych materiałach – podkreśla Michał Olejarczyk.
O projektach Rapid Troopers można poczytać także na stronie internetowej koła i jego profilu na Facebooku. Studenci planują też uruchomić streaming ze swojego warsztatu. Dzięki zamontowanej tam ruchomej kamerze, każdy będzie mógł poprzez stronę internetową obejrzeć, jak wygląda drukowanie 3D i zerknąć, czy w warsztacie ktoś pracuje i nad czym.
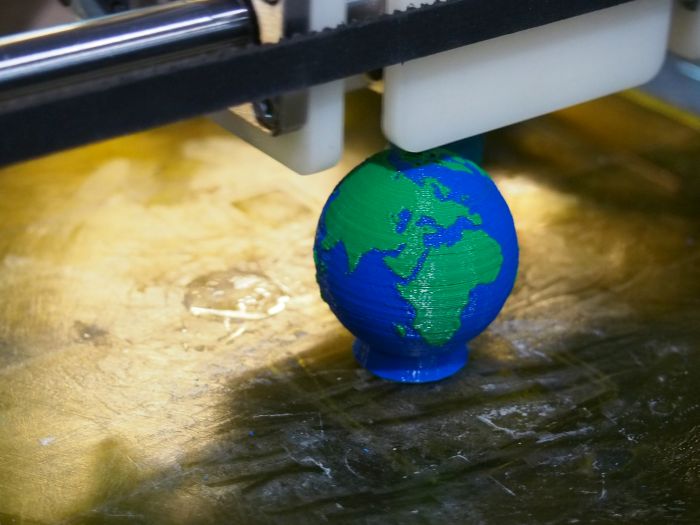
Koło działa na Wydziale Mechanicznym PWr. Jego opiekunem jest dr Tomasz Boratyński. Przy części projektów – wymagających interdyscyplinarnych zespołów – pracują także studenci z Wydziału Elektroniki.
Lucyna Róg